Innovative Sol-Gel Coating Solutions for Extraordinary Performance
SOL-GEL OVERVIEW
WHAT MAKES E-14 DIFFERENT?
E-14 is unique as it does not require mechanical abrasion for adhesion, it bonds chemically.
E-14 does not require a high film build for durability and performance; less film build is actually optimal.
E-14 is highly chemically resistant, abrasion resistant and corrosion resistant.
E-14 is inert and will not react chemically when cured.
E-14 is an inorganic compound, meaning we are based on creating coatings without carbon-based chemistry.
E-14 “plays well with others” as our primers and topcoats can be used with other chemistries to create new products or coating systems.
E-14 is fully oxidized upon cure, which also makes it UV stable*
E-14 can be a custom fit, need a specific application? We can help with that!
*UV transmission that may affect the underlying layer can still occur.
WHY E-14 PRODUCTS?
E-14 Polymers Are Industrial Grade Products Specified For Manufacturing & Industrial Applications
E-14 Polymers: Chemically Bonded for Superior Performance
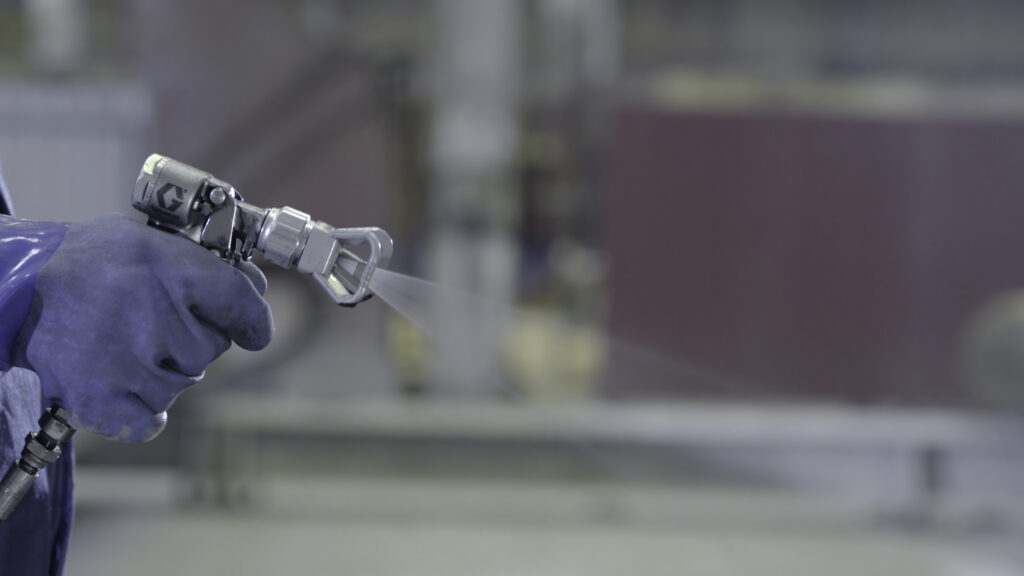